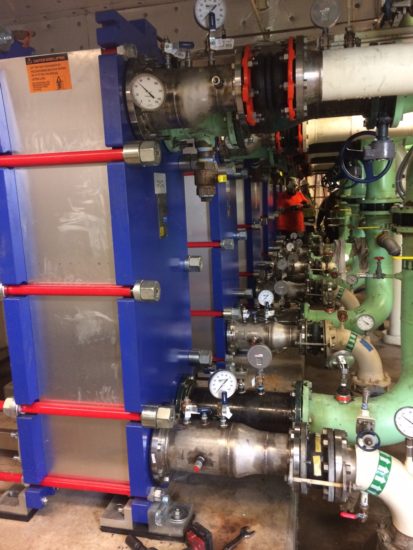
The last few months were quieter than usual for ALS users but not for staff tasked with maintaining and improving the ALS. The recent ALS shutdown was one of the longest on record, spanning almost three months. Those involved say it was also one of the most successful, with everything on the to-do list crossed off. The work accomplished paves the way for new beamlines, better water-cooling capacity, and ALS-U.
The biggest shutdown projects this year were in Sectors 2 and 3. Sector 2 was prepared for the insertion device that will provide light to the new protein crystallography beamline, Gemini, and the third harmonic cavities were relocated from Sector 2 to Sector 3. The magnetic and vacuum systems group also installed a new fast DOE kicker in Sector 2, which will be key to ALS-U development, as it will enable on-axis injection. On-axis injection will allow the electron beam to be transferred to the storage ring without large horizontal oscillations.
The fast kicker employs two parallel strip-line electrodes on each side of the stored beam. The electrodes shape a pulsed electromagnetic field that kicks the beam, allowing injection and extraction. “We had to demonstrate that we could put electrodes within 3 mm of the beam without damaging them, and it worked,” says ALS Magnetic and Vacuum Systems Group Leader Chuck Swenson. “The thermal data on the new kicker device is already encouraging; it runs much colder than the old camshaft kicker that was in place.”
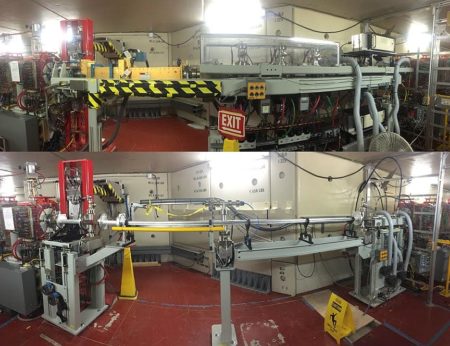
The key to the Sector 2 work was clearing space to set the stage for the arrival of the Gemini undulator, making it straightforward to install in a future shutdown. “We had to tear out quite of bit of the accelerator,” says Swenson. “It was daunting to trust that we could pull out that much and put something back in that was actually going to work, but we did.”
Swenson points out that it was the close collaboration and coordination between five different ALS groups—the vacuum group, radio frequency (rf) group, mechanical engineering group, survey and alignment, and electrical group—that made this work successful. And, of course, many months of advance planning. “It was impressive to see everyone work together and deal with the bumps along the road,” he says. “I tip my hat to our teams in terms of how we operated during this process; everything went so well.”
The final step in the many-years-long storage-ring rf upgrade project happened in parallel with the other Sector 2 work. The upgrade project converted all of the storage ring’s low-level controls from analog to digital. “The success of this project really moves us from unreliable old technology to current technology, which allows for better control, but it’s been very challenging to accomplish,” says ALS Project and Facility Management Lead Steve Rossi.
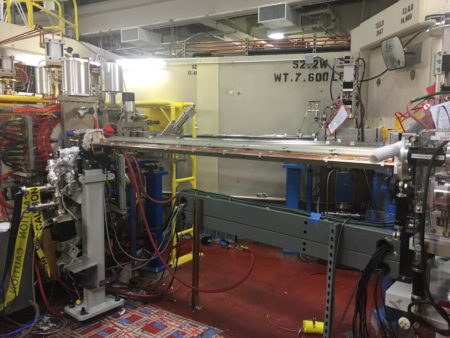
The other big shutdown project was in Sector 7, where staff installed a new non-evaporable getter (NEG)-coated vacuum chamber and an undulator for the Coherent Scattering and Microscopy (COSMIC) beamline. The project marks the first NEG chamber to be installed at the ALS, and its success bodes well for ALS-U. The NEG chamber allows the beam to reduce to a very small gap, which in turn allows the undulator to meet its target.
ALS mechanical technicians were also tasked with rebuilding an elliptically polarizing undulator and installing it in Sector 4. The ALS has about 15 mechanical technicians (or “mech techs,” as they’re better known around the ALS) on staff, and “borrows” more through matrixed divisions during shutdowns. “We have four technicians who’ve been here since day one, since first light at the ALS,” says Mechanical Technology Engineering Leader Dan Colomb. “That’s part of what makes things go so well; that depth of knowledge and history with the equipment.”
From a mechanical engineering perspective, the biggest challenge of this shutdown was that the mechanical technicians had to vent about 70 percent of the storage ring, says Colomb. “The storage ring operates in ultrahigh vacuum (UHV), so when we vent it we have to be very careful not to put any contaminants into the vacuum chamber,” he says. “We don’t have the option of cleaning or baking the storage ring, so each time we vent it we have to be very careful.”
The replacement of the low-conductivity water (LCW) cooling towers was probably the most visible shutdown project. The huge towers are located along the side of Building 6, and the construction work there was responsible for the loss of some precious parking spots over the last couple months. The ALS uses about 3,000 gallons per minute of LCW for cooling and requires great stability in terms of both flow and temperature. The Berkeley Lab Facilities Division led the charge on replacing the towers, which was fraught with weather delays; the project lost 21 days due to rain. But the new cooling tower is up and running. The remainder of this project consists of installing new LCW pumps, as the older ones aren’t capable of pumping the required capacity to meet LCW needs. There is still significant construction the LCW plant remaining—once the current pump work is complete in a few weeks the demolition of the old towers will take place and a second new tower will be installed and then commissioned at a later time. When the work is complete the ALS will have 800 tons more capacity than the old plant and fully redundant towers for improved reliability.
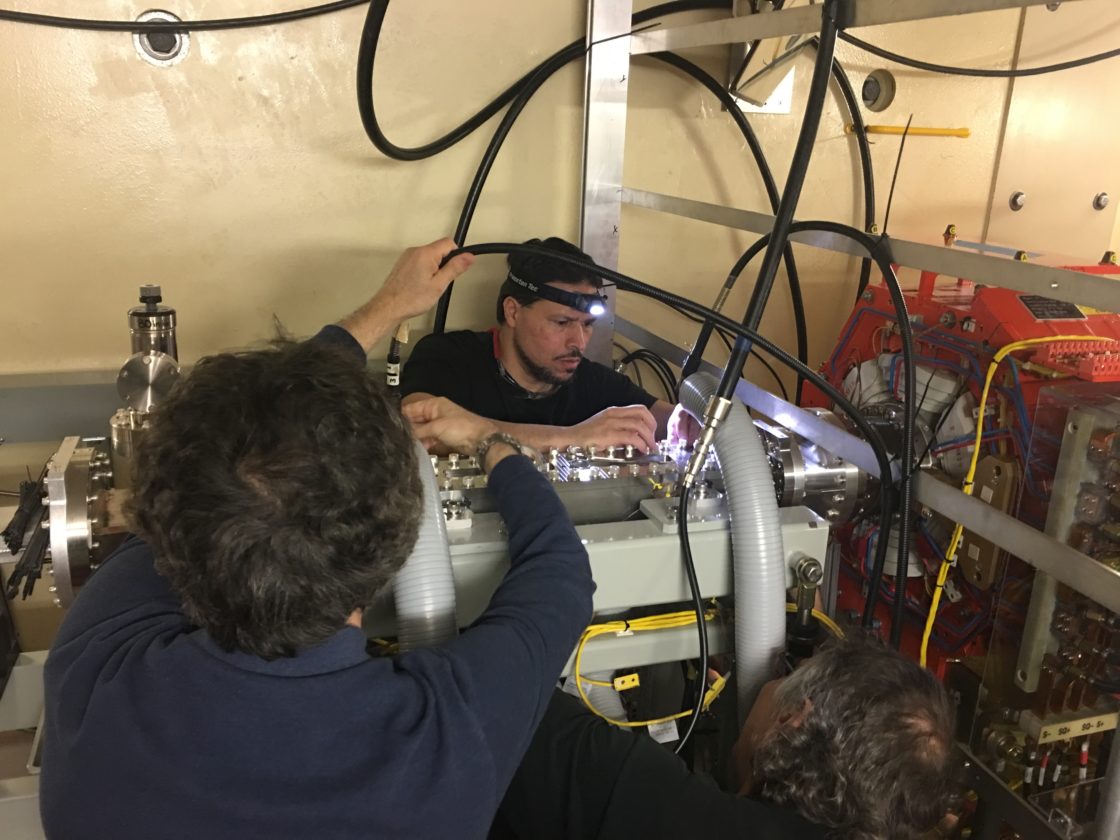
Though much of it is behind the scenes, the shutdown process takes eight to ten months of planning and furious production and fabrication before the more visible installation and upgrade work begins, all of which involves many people coordinating and communicating effectively.
“Along the way there are inevitably things that don’t fit and we’re always working very closely with engineering, because there are modifications that have to be made in the field or we have to use new or different parts,” says Colomb. “There are always going to be things we can’t predict ahead of time, but our excellent teams manage this so well.”