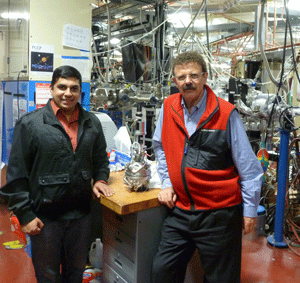
LBNL senior materials scientist and U.C. Berkeley professor Rob Ritchie has been researching the fracture behavior of a wide array of materials for the past 40 years, the last ten of them using the facilities at the ALS. From human bone to synthetic engineering materials such as shape-memory metals and composites, Ritchie has illuminated groundbreaking cracking patterns and the underlying mechanistic processes using the x-ray synchrotron micro-tomography at ALS Beamline 8.3.2.
One of Ritchie’s latest materials research projects is contributing to the evolution of jet engine performance, and hence has industry players heavily interested and invested. Termed ceramic-matrix composites, the materials that Ritchie, specifically with his post-doc Hrishikesh Bale, are now studying can withstand temperatures that would melt current state-of-the-art engine material, alloy-based nickel.
The heat-resistant properties of advanced ceramics materials has been known for a long time, but the materials’ poor resistance to fracture has always been the major drawback to their use as structural materials. But this new generation of ceramic composites is the emerging material of choice for next-generation gas turbines and hypersonic-flight applications due to their added strength and temperature resistance without catastrophic failure.
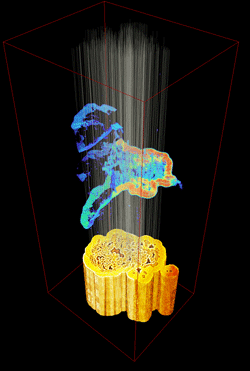
Ritchie and his group are currently probing the depths of ceramics composites’ fracture and temperature resistance at Beamline 8.3.2 as part of a collaborative research project with Teledyne, funded by NASA and the U.S. Air Force. Ritchie’s team, which includes his post-doc Hrishi Bale and a team of ALS beamline scientists headed by Alastair MacDowell, have developed a unique facility that permits mechanical testing of these composites at very high temperatures with simultaneous real-time 3-D imaging of materials.The inherent brittleness of ceramics has been overcome in the new composite materials by creating hybrid microstructures. Because of the complexity of their design, they have the toughness to resist cracking at ultrahigh temperatures in extreme environments. The key to the materials’ safety is how the microstructure can contain and impede the growth of numerous small cracks that are created when loads are applied at high temperatures, i.e., how much damage they can withstand under these extreme conditions. The tomography facilities at the ALS allow Ritchie and his colleagues to study this process in 3-D with a spatial resolution below one micrometer, under load and at temperature.
“The nickel-based superalloy materials that are currently used in our gas-turbine engines have reached the absolute limit of their temperature range,” says Ritchie. “But if new engines can be designed to operate safely with these new ceramic composite materials, the potential payoff would be enormous and lead to major breakthroughs in engine performance.”
Ritchie thinks that we will see ceramic composite engines on the commercial market within the next ten years or so. “Ceramic composite engines could achieve a 10 to 20 percent or more weight reduction from current engines, with much increased efficiencies, which translates into considerably lower fuel consumption and reduced environmental pollution” says Ritchie.
With the testing facility they’ve developed at the ALS tomography beamline, Ritchie says they’ve moved past an important milestone in the research process: how to study and mechanically test these ceramic matrix materials at such ultrahigh temperatures.
“We’re getting measurements of the mechanical properties at temperatures that are literally unprecedented, coupled with wonderful 3D images and quantitative data of the damage under load, all results that can be accurately used to provide future predictions of the structural integrity and safe lifetimes of the exciting new materials,” says Ritchie.