Through a collaboration with two Berkeley Lab user facilities as well as two other national labs, a small Bay Area company has made big news in the semiconductor world. Modern electronics are getting smaller and smaller, which means the demands on semiconductor manufacturers are increasing. To ensure the quality and consistency of substrates, wafer manufacturers employ metrology tools to control the quality of their materials, but those tools are not as precise as the industry needs. Last year, Hayward-based aBeam Technologies made history with the development of the finest metrology tool in the world, utilizing a fabricated pattern with line widths down to 1.5 nanometers. The collaborative efforts of Berkeley Lab’s ALS and Molecular Foundry, Argonne National Laboratory, Brookhaven National Laboratory, and aBeam Technologies on this “binary pseudo-random calibration tool” earned them a 2015 R&D 100 Award.
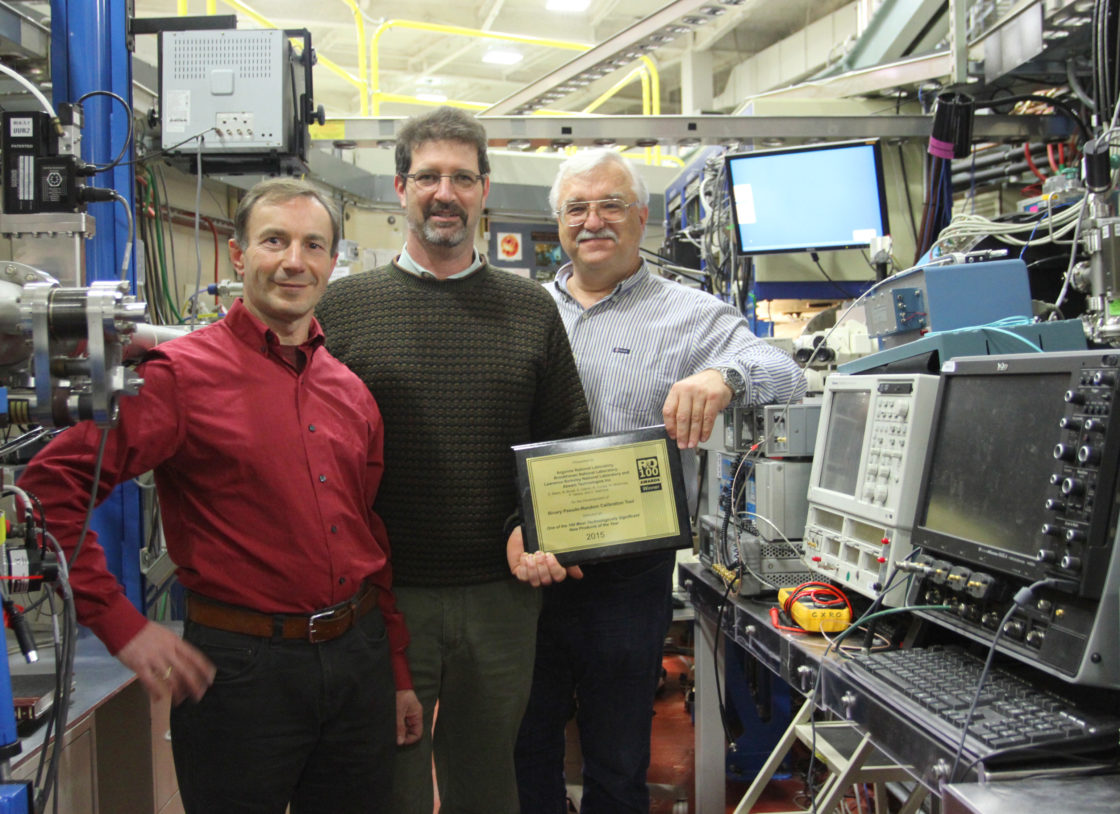
As Moore’s Law progresses and the semiconductor industry moves into the next phase of precision, new metrology instrumentation is a requirement for success. The binary pseudo-random calibration tool, which can be used for calibrations of a broad range of metrological instruments, was based on a patent that had been filed by ALS and Brookhaven back in 2009. aBeam relied heavily on ALS capabilities for the tool’s metrological features and the Molecular Foundry for fabrication equipment. A DOE grant has given the small company the funds required to commercialize the groundbreaking technology.
The technology applies a variety of test samples and analytical methods to the evaluation and calibration of advanced metrology instrumentation with resolution from millimeters down to nanometers. It solves one of the most difficult problems in metrology techniques: the quantitative characterization of the imaging instrumentation. The calibration technology has already found several applications at national laboratories. The technology has become part of a process used by the ALS for tuning and characterizing x-ray microscopes. It has also allowed precise calibration of the surface metrology profiles for state-of-the-art x-ray optics at the Center for X-Ray Optics.
“When you measure anything, you have to be sure that your metrological system produces accurate results, otherwise what kind of results will you get, nobody knows,” says ALS Staff Scientist Valeriy Yashchuk. “Qualifying and tuning metrology systems at the nanoscale is not easy, so we designed a test pattern that is capable of characterizing nano-metrology systems over their entire dynamic range, resulting in the modulation transfer function, the most comprehensive characteristic of any system.”
aBeam has a long history of collaboration with the Molecular Foundry, relying on state-of-the-art nanofabrication equipment and utilizing the expertise and advice of the Molecular Foundry’s Nanofabrication Facility Director Stefano Cabrini. aBeam began working on this technology about a year and a half ago at the Molecular Foundry. “It was a very successful collaboration; really a paradise for us,” says Sergey Babin, president of aBeam Technologies.
After fabrication comes testing and verification, and for this aBeam turned to the ALS and guidance from Yashchuk at Beamline 6.1.2. “The characterization of our samples on the soft x-ray microscope at the ALS was one of the most valuable parts of our experience there,” says Babin. “And we helped them as well, because our test samples verified the resolution of the ALS microscope.”
“The fabrication and the verification are the most difficult parts of this technology,” says the Foundry’s Cabrini. “A small company cannot do this by themselves; they need facilities like the Foundry or the ALS to do this.”
Likewise, the Foundry and the ALS were not in a position to commercialize the potential in a technology like this, so aBeam knew it would have to. “But for us as a small company it was too big an investment,” says Babin. “So, along with the ALS and the Foundry, we applied for a special DOE commercialization grant that is specifically intended to be used to make a product out of a patent and take this product to market.”
aBeam received the grant, which has allowed them to continue to develop a full product based on the technology, with fabrication happening at the Foundry and all the metrology and testing done at the ALS. “Feedback is essential for us to move this forward, and we get great feedback here at the ALS and the Foundry,” says Babin. “The success has been overwhelming at this point.”
aBeam plans to start phase-one commercialization within the next six months. They have another year to go on their grant, and plan to release a full turnkey commercial product, including equipment and software, in one year. Metrology is a multibillion-dollar industry that is an indispensable part of science and manufacturing, and aBeam’s customers include the top names in the semiconductor industry. “Our product will allow any engineer or technician to easily characterize metrology equipment in the full dynamic range of the equipment,” says Babin. “Right now companies are competing with characterization methods that are very vague, and this will change that dramatically.”
“There is a huge need for a standard like this—something that can calibrate resolution,” says Cabrini. “Right now there really is no way to be sure about comparisons, because every company has developed their own way to characterize, and they may have chosen the method that’s the most beneficial to them.”
Cabrini also points out that there is a huge scientific interest in the product. He and his team have already used it to measure resolution on some of their equipment, and the ALS has done the same at beamlines. Both facilities continually benefit from helping aBeam move their product forward.
“It’s a win-win situation; we are benefiting scientifically from their research and they are benefiting hugely from being able to use our facilities and just from their association with the Lab,” says Cabrini. “The fact that Sergey [Babin] can go out and say that this product has been tested and validated by LBNL is a huge plus.”
“It’s been a really tight, very broad collaboration between us, the Foundry, and aBeam, as well as our colleagues at Argonne and Brookhaven,” says Yashchuk. “Amazingly successful.”