Developing ceramic matrix composites (CMCs) to replace the metal alloys traditionally used in jet engines has been a goal for the aviation industry for decades. CMC-based components allow engines to operate at higher temperatures, which promises improved efficiency and performance. But understanding and controlling CMCs’ behavior is key to have the confidence necessary to use them in engine production. For more than a year, GE Aviation has used the tomography capabilities at ALS Beamline 8.3.2 to gain insight into their CMC materials, guiding their engineering and design efforts.
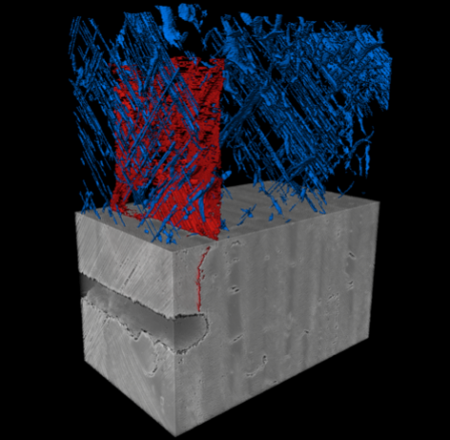
GE Aviation has been researching CMC materials for more than 20 years and recently made major strides in their application with the introduction of new CMC-based jet engine components for commercial aircraft. The CMCs GE Aviation has researched at the ALS are made of woven silicon carbide fibers impregnated by a ceramic resin, manufactured through a highly sophisticated process, and further enhanced with proprietary coatings. They are one-third the density of traditionally used metal alloys but they maintain comparable strength to alloys currently used in engines up to higher temperatures and so allow gas turbines and jet engines to run hotter, offering the economic and environmental advantages of higher fuel efficiency.
Despite the increasing use of CMCs in extreme environments such as jet engines, the fundamental and quantitative links between the processing conditions, the resulting microstructure, and the long-term structural performance remain largely undiscovered. In an effort to further understanding, a group of researchers from academia, industry, and government established an Approved Program (AP) at the ALS to use novel synchrotron radiation microtomography experiments at Beamline 8.3.2 to gain insight into the entire life cycle of CMCs.
APs enable an investigator or group of investigators to carry out an extended program of research in partnership with ALS staff. This three-year AP, awarded at the end of 2015, brings together researchers from the University of Utah, UC Berkeley, GE Global Research, GE Aviation, Teledyne Scientific, the Air Force Research Laboratory, and Lawrence Berkeley National Laboratory for the common goal of discovering processing-property-performance links in CMCs and enhancing the existing capabilities of Beamline 8.3.2 to enable ongoing and future imaging and in situ efforts.
“It’s been really exciting to see an Approved Program that’s a partnership between industry, academia, a Department of Defense laboratory, and a Department of Energy national lab,” says Beamline Scientist Dula Parkinson. “I don’t know of another AP at the ALS that has all of those components.”
This AP builds on years of CMC research at the ALS, much of which has been led by Berkeley Lab scientist Rob Ritchie and his research group. Ritchie, in close collaboration with ALS staff, was responsible for developing and instituting the ultrahigh-temperature tomography facility at the ALS, which is what drew GE Aviation and the other members of the AP to the ALS. (See this LBNL news release and this Nature Materials paper for more on Ritchie’s groundbreaking research at the ALS.)
The capabilities developed by an AP often have lasting impact that go beyond the program’s partners. Parkinson says that the CMC program has provided new equipment at Beamline 8.3.2 that benefits all of the beamline’s users. “They’ve been the drivers behind developments in both new hardware and new software,” he adds.
Data analysis and management have been major challenges for GE’s work at the ALS. “We are facing a daunting task of having to understand terabytes and terabytes of data and construct a model of this material,” says Greg Wilson, a senior engineer in GE Aviation’s Composite Materials Behavior group. “The folks at ALS have been very helpful with that.”
“Since there’s so much interest in these materials, we really want to provide a streamlined data analysis process,” says Parkinson. “Daniela Ushizima, Talita Perciano, and Harinarayan Krishnan, scientists in Berkeley Lab’s Computational Research Division (CRD), have been instrumental in leading development of new image analysis tools that really enhanced our capabilities at the beamline—building algorithms that have automated feature extraction and measurement, greatly speeding up what used to be a painstaking manual process.”
The CRD scientists are part of the joint ASCR-BES Center for Advanced Mathematics for Energy Research Applications (CAMERA). CAMERA’s charge is to bring new applied mathematics to bear on advanced data analysis problems at DOE beamlines.
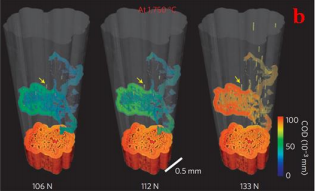
As a part of the AP, GE Aviation has been able to test CMCs, gather deep insights, and enhance their engineering efforts as they move forward with CMC-based engine components in commercial production. GE has been using Beamline 8.3.2 for mechanical testing to look at CMCs at the sub-micron scale, gaining a better understanding of their features and the interaction between microstructure and damage evolution.
“By getting down to the microstructure of the features in these materials, we’re able to better predict the behavior of the materials,” says Wilson. “The ALS lets us test these materials in extreme environments, while being able to image in real time to see the materials perform, at micron-level resolution.”
“We can see how individual constituents of these materials behave,” he adds. “There aren’t too many places in the world that offer the ability to do this type of analysis; the ALS is unique.”
Wilson says that GE’s goal for their work at the ALS is to push their CMCs to the point of failure so that they’re able to see where the weaknesses are and have their engineers and designers integrate that data into their work.
“With the increasing complexity of these materials that we’ve developed over the last four years, it’s really helpful to be able to look at the physics of how the fibers in the composite interact with their coatings and with the matrix and come together to give it its properties,” says Wilson.
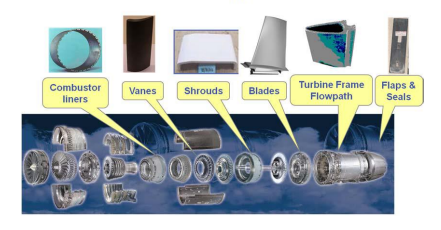
Understanding more about the CMCs through ALS research also helps GE in the manufacturing process, says Wilson. GE Aviation has established a CMC supply chain in the U.S. that includes CMC raw material production (Huntsville), research and low-volume production (Cincinnati), the CMC Lean Lab where GE perfects the manufacturing process (Delaware), and CMC mass production (Asheville). GE Aviation’s CMC engine components are now in production in LEAP commercial jet engines, designed specifically for narrowbody aircraft and produced by CFM, a joint venture between GE and Safran Aircraft Engines.
CMCs have long been a key element in GE Aviation’s strategy to improve performance and reduce cost of ownership in advanced turbine engines for both military and commercial applications. Throughout jet engine propulsion history, the average rate of technology progress for turbine engine material temperature capability increased 50 degrees F per decade. With the introduction of CMCs, GE will now increase 150 degrees F this decade.
Adds Wilson, “GE Aviation has made a big bet on CMCs, and our bet is paying off.”