TE Connectivity is a world leader in connectivity—the $13 billion global company designs and manufactures more than 500,000 different electronic connectivity products for the automotive, energy, industrial, broadband communications, consumer device, healthcare, aerospace, and defense industries. TE Connectivity has a long-standing commitment to innovation and engineering excellence. Their products help address challenges arising from companies’ need for energy efficiency, always-on communications, and ever-increasing productivity. Recently, a team led by TE’s senior manager of materials development, Dr. Jerzy Gazda, has been investigating how ALS tomography capabilities can help the company develop more efficient connectors.
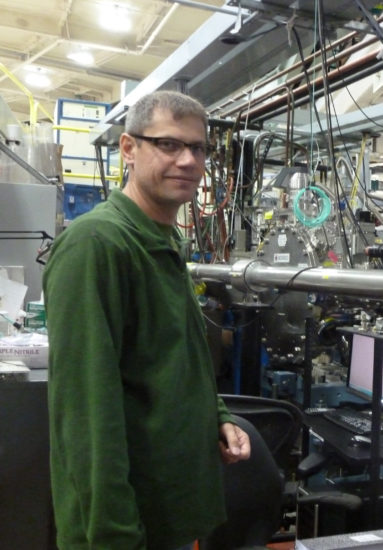
Gazda, who oversees one of the materials development teams for TE, began working at the ALS in May 2013, conducting prototypical studies that he and his group plan to use to develop a larger proposal for an ALS-TE industrial partnership. Gazda describes his work at the ALS as “forward-looking, basic sciences research,” much of which will be non-proprietary.
The TE researchers have focused much of their initial investigative research at Beamline 8.3.2 on the use of recycled polymeric resins in connector housings. The company purchases engineered resins each year and recycles residual materials. While TE is committed to using recycled materials, one challenge is that the performance of recycled materials is not as predictable as that of virgin materials. For example, in virgin polymeric resin, reinforcing glass fibers are distributed in a predictable pattern throughout the material, whereas when recycled materials are incorporated, the size distribution of the fibers is more random and can lead to significant changes in the flow and strength of the polymer. The effects become even more complex with additional reuse cycles.
“With recycled resins, we are facing additional variables in the injection molding process,” says Gazda. “The ALS can help us understand the limits of adding recycled materials to our products—with the unique resolution of 3D-CT tomography available at the ALS, we can see how the fibers align. That will help us model and predict how these materials behave in the manufacturing processes and during the lifetime of the connector housings.”
Polymeric resins are used in the housings for the connectors TE produces for a number of industries. The use of recycled resins in TE’s products would help the company reach their sustainability goals and save money, while reducing materials and energy waste overall, says Gazda. Beamline 8.3.2 tomography facilities are helping TE build a case for how much recycled resin can be incorporated into their products while maintaining high quality standards.
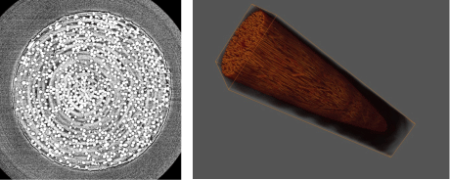
“It’s the structural questions that the ALS answers for us,” says Gazda. “The sub-micron resolution that we get is phenomenal; it literally allows us to look inside fragments of the connector housings.”
The company is interested in furthering these studies, which would eventually advance to the stage of proprietary research. In anticipation of increased interactions and collaborative research at the ALS, TE is forming a multi-disciplinary team that would be responsible for analyzing the data that comes out of the company’s beamline research.