We generate staggering quantities of plastic and plastic-containing products each year, but only a tiny fraction of that plastic can be recovered and used to manufacture products of similar quality. That’s because most products are made from mixtures of different plastics. Once they are mixed, those plastics can’t be recovered and most of it ends up in landfills, incinerators, or oceans. Scientists are tackling this challenge using a custom-designed material called polydiketoenamine (PDK), a new type of plastic developed to be recycled efficiently and indefinitely.
“We now know how to tailor PDK plastics in order to recycle complex products comprising several types of materials,” said Brett Helms of Berkeley Lab’s Molecular Foundry, who led the study. “An example might be a shoe, where a textile is bonded to a rubber by an adhesive. Conventional materials used in such products can’t be recycled for reuse, since they can’t be deconstructed independently. Yet, if they were made from different, specially designed PDK polymers, then they could be for the first time.”
The researchers made a variety of PDKs with slightly different chemical structures and showed that each could be “depolymerized,” or broken down to its respective monomers, with high yields of recovery at different temperatures and rates. At Advanced Light Source Beamline 12.2.1, the researchers used single-crystal x-ray diffraction to determine the structural differences between the engineered monomers. Theoretical calculations performed by scientists at Berkeley Lab’s Molecular Foundry provided valuable insights that led to further optimization.
Using those optimized molecules, the researchers created blended PDK plastics and then completely depolymerized and recovered the constituent materials. With a slightly more complex process, they repeated the demonstration with PDKs of different colors, addressing a particular industry challenge.
Finally, the researchers successfully demonstrated the high-yield recovery of PDK monomers, as well as glass and stainless steel, from an object designed to simulate the challenges of automobile recycling. These results could lead to a meaningful shift in how we approach the manufacture of durable goods, enabling a circular economy in which products are designed to be fully recovered and reused.
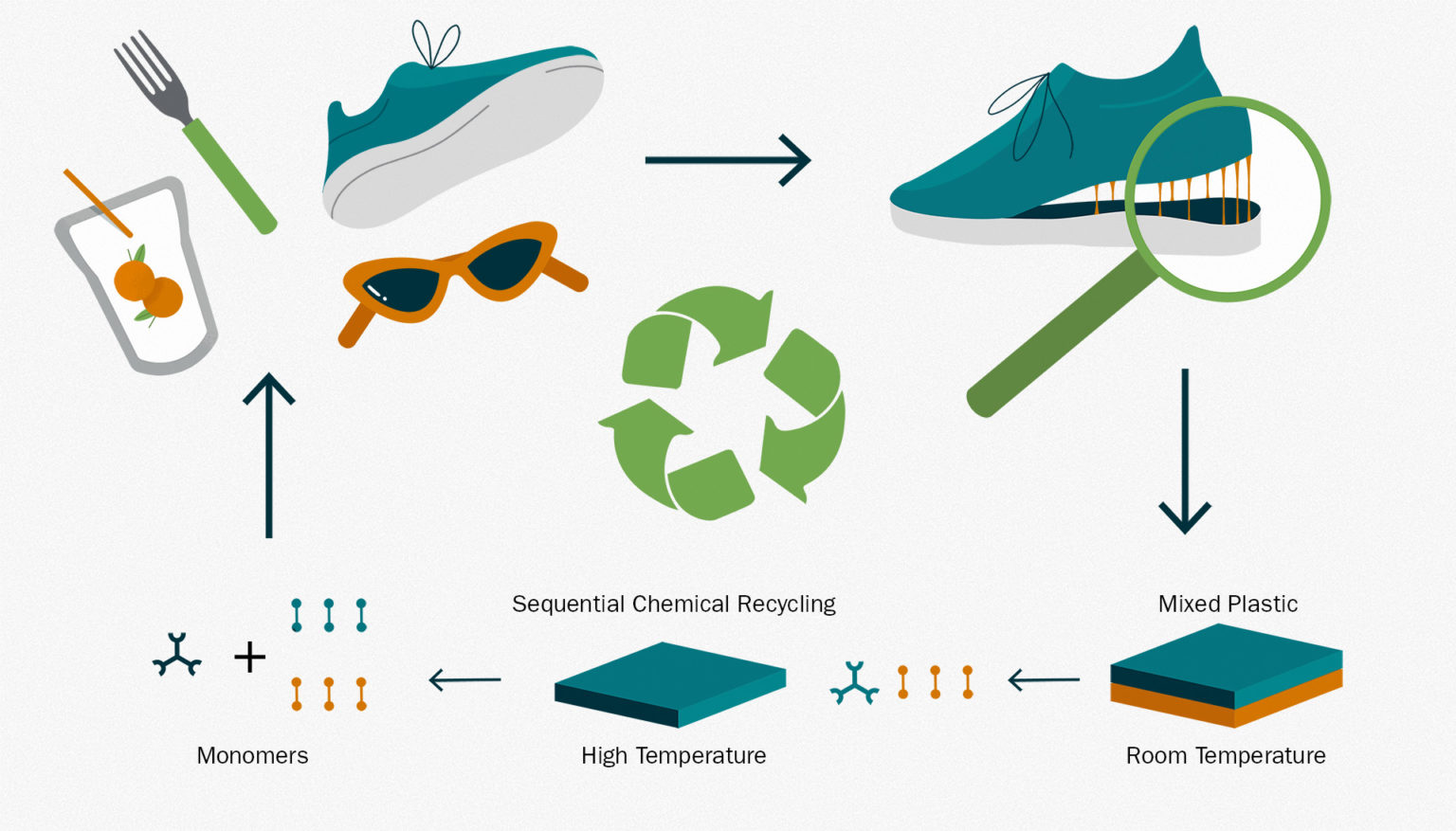
J. Demarteu, A.R. Epstein, P.R. Christensen, M. Abubekerov, H. Wang, S.J. Teat, T.J. Seguin, C.W. Chan, C.D. Scown, T.P. Russell, J.D. Keasling, K.A. Persson, and B.A. Helms, “Circularity in mixed-plastic chemical recycling enabled by variable rates of polydiketoenamine hydrolysis,” Sci. Adv. 8, eabp8823 (2022), doi:10.1126/sciadv.abp8823.
Adapted from the Berkeley Lab news release, “Designer Materials to Keep Plastic Out of Landfills.”