In the chemical environments common in energy production plants, steel pipes and equipment can accumulate layers of iron sulfide, some of which are corrosion resistant and provide protection to the steel surface. Understanding how operating conditions affect steel surface layers can improve corrosion rate estimates, decreasing building and maintenance costs, and increasing the safety and reliability of operating plants. Chevron Energy Technology Company (Chevron ETC) is currently studying the link between operating conditions and corrosion properties at Berkeley Lab’s Advanced Light Source (ALS) Beamline 12.3.2 to determine which corrosion layers form and in what order.
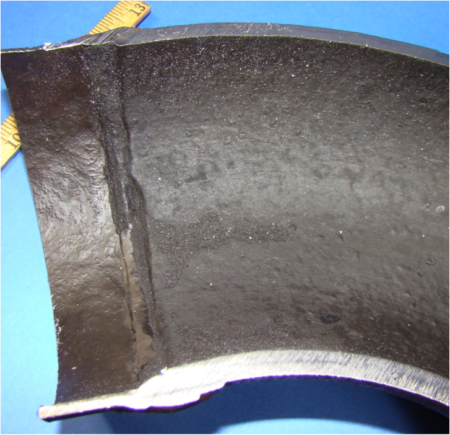
Corrosion layers, or scales, form on construction materials like steel as a result of corrosion reactions that take place between the steel and the process fluids in production plants. Exposure to different process chemistry can affect the type of scale that forms, varying in the presence of minor phases, oxide layers, and incorporation of minor alloy additions such as silicon into scales.
“Under some conditions, iron sulfide scales are very reliable,” says Monica Barney, research engineer at Chevron ETC, who has been conducting the corrosion experiments. “When sulfur compounds first react with the material, an initial layer forms which protects the material, slowing down the corrosion rate and preventing more reaction.”
However, under other conditions, the scales are not protective. Rust, for example, forms when moisture from the air reacts with steel, forming certain iron oxy-hydroxides that flake off and eventually ”rust away” the base metal. Barney’s group is comparing protective and non-protective sulfur scales found in the field to those created in a lab to gain a better understanding of which scales are protective and why. The results of their studies will inform the development of corrosion inhibition via improved coatings, changes in composition, or other variables.
“Right now, we know steel corrodes when we expose it to various environments, but the exact underlying mechanism is not known for each condition,” Barney says.
Some pieces of equipment show different corrosion scales in different areas. Though both are constructed from steel, a pipe and the elbow attached to it may have undergone subtle differences in processing, or may have different compositions that cause them to react differently to the same environmental conditions and form different scales. “Over time that can have a measureable effect,” says Barney.
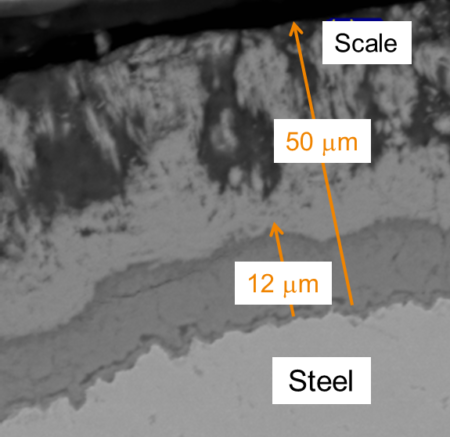
At the ALS, Barney can directly compare structural differences in layers to find which are protective and what it took to create those layers. This could yield insight into which production techniques and operating conditions will extend the life and reliability of equipment and protect the safety of workers. Better estimates of corrosion rates will help management plan when to shut down the plant to replace parts, she says.
Barney’s division focuses on safety and reliability. “Because of this focus, we sometimes make information public and work directly with our competitors to solve problems,” she says. “We just want to improve safety.”
This approach is what brought her research to the ALS. Unable to conclude their studies in Chevron ETC research facilities, Barney suggested that her group use micro-diffraction at the ALS. She has a long history as an ALS user, having done her Ph.D. research at Beamline 7.3.3.
“What’s so unique about Beamline 12.3.2 is that while the synchrotron itself collimates the x-rays to an amazing level, 12.3.2 has an even smaller spot size,” Barney says. “In fact, whatever accelerator physics did during your shutdown in February was fantastic! Since we collected data here last August and then again in April, we could make a direct comparison and it made a phenomenal difference for us.” She will be here again in November.
Barney (at left) uses Beamline 12.3.2 because it has the spatial resolution necessary to look at each layer. There are many variations of iron sulfide, including many meta-stable phases, so the element ratio doesn’t reveal what is actually in the scale. Barney used to guess at the interface location when setting up her experiments, but with the most-recent ALS upgrade, spatial resolution can be maintained in a new sample orientation that allows for detection of both fluorescence and diffraction signals. This adds a visual aid during diffraction that gives Barney “a vivid map of exactly where the interface is.” She can now ensure the x-rays hit just the right spot on the sample (containing steel, scales, mounting compound, etc.), guaranteeing data collection on the interface of interest, and greatly improving speed, precision, and accuracy. Data collection is now so fast they have a deluge of data to analyze.
Barney will also be using Beamline 8.3.2 to look at the through-thickness porosity of coatings applied to materials to learn which coatings have channels by which corrosive agents can reach the surface of the material. She is interested in how the channels line up in these protective layers and whether there is a 3D path that reaches the metal surface. Using ALS tomography capabilities, she will be able to see what grows in the channels and study reactions under various conditions.