Cement production – the mainstay of the modern concrete industry – is one of the primary sources of carbon dioxide emissions worldwide. Making cement essentially requires burning rock, an extremely energy-intensive process that releases a large amount of carbon into the atmosphere. In an effort to reduce its carbon footprint, the industry has begun to move toward new concrete “recipes” that incorporate environmentally friendly supplemental cementitious materials (SCMs), which partially replace Portland cement and reduce its use. The challenge is to maintain, or even increase, the end product’s strength and durability while becoming more environmentally sustainable. Ancient Rome, without the impetus of modern environmental concerns, had a lot of this figured out. New insights into the Romans’ ingenious concrete harbor structures now emerging from ALS beamline research could move the modern concrete industry toward its goal.
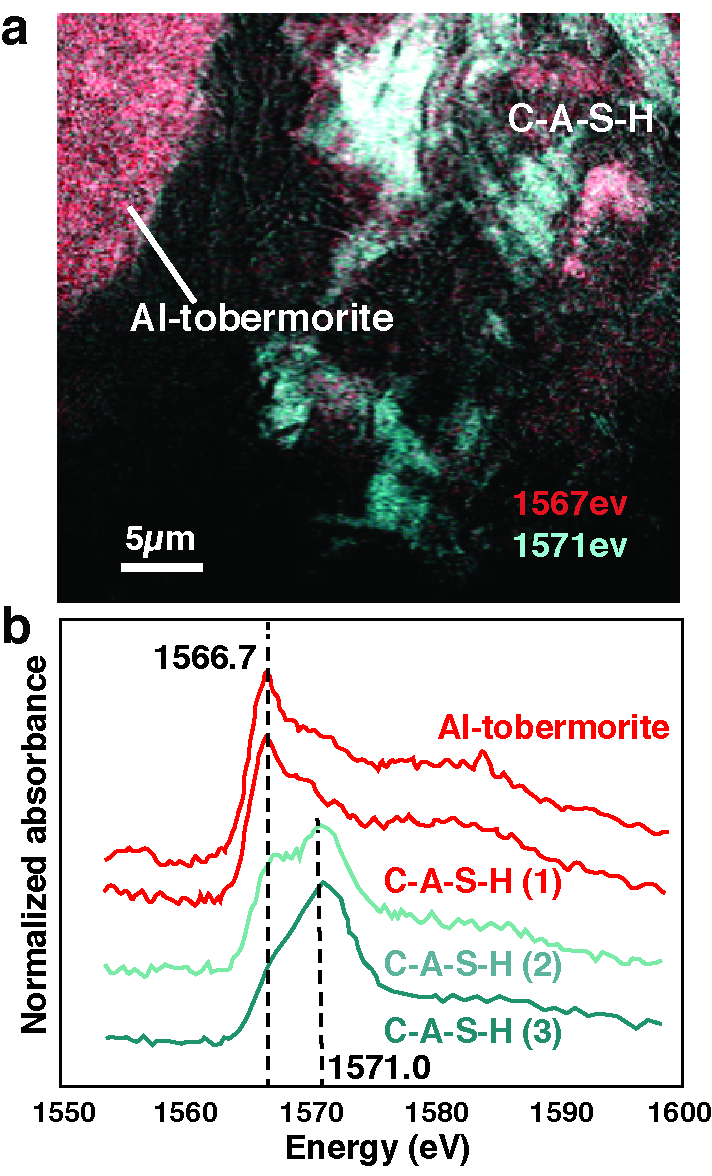
Through analyses at ALS Beamlines 12.2.2, 12.3.2, 5.3.2.1, and 5.3.2.2, Marie Jackson, a UC Berkeley research engineer and part of an international research team sponsored by global concrete company C.T.G. Italcementi and the ROMACONS research team, saw for the first time how an extraordinarily stable compound called calcium-aluminum-silicate-hydrate (C-A‐S‐H) plays an integral role in the structure of Roman seawater concrete, binding together a material that is still strong and stable after 2,000 years exposure to aggressive marine environments. Most modern concrete relies on Portland cement, which hydrates to form a silicate-hydrate (C-S-H) binder. Many such structures are showing signs of decay after just 50 years, especially in maritime environments.
Research from Beamline 5.3.2, in collaboration with UC Berkeley researcher S. Rosie Chae, revealed that the specific way the aluminum substitutes for silicon in the poorly crystalline C-A-S-H structure may be the key to the cohesion and stability of the seawater concrete. In addition, the principal crystalline cementitious component in every one of the eleven Roman seawater concrete harbors drilled by the ROMACONS team is a mineral called Al-tobermorite, which provides the model basis for C-A-S-H. The Al-tobermorite is produced by reaction of seawater, lime, and a particular volcanic ash that the Romans used in their concrete mixture.
“Cement chemists first doubted our observation that there was real Al-tobermorite in the Roman seawater concrete. That’s because this is a high-temperature geothermal mineral that is usually synthesized at higher temperatures than what’s produced in conventional concrete,” says Jackson. Its material properties have never been measured, but Jackson was recently able to carefully excavate the mineral from samples and learn more about how it behaves through experiments with Juhyuk Moon, an assistant professor in Civil Engineering at Stony Brook University, New York, at Beamline 12.2.2. The very fine Al-tobermorite crystals and a zeolite mineral, phillipsite, in the cementitious matrix were described at Beamline 12.3.2. Jackson’s ALS findings form the basis for a new paper that was published this month in American Mineralogist titled “Unlocking the Secrets of Al-Tobermorite in Roman Seawater Concrete.” She and her team have also published another paper, “Material and Elastic Properties of Al-Tobermorite in Ancient Roman Seawater Concrete,” in the June 2013 issue of the Journal of the American Ceramic Society, based on her ALS research.
“We have a lot of new information for modeling long-term behavior of sustainable concretes that use aluminous cementitious materials, thanks to the Romans and the ALS,” says Jackson. “At all three beamlines, we’ve gotten really unique information that we would not have gotten elsewhere and the beamline scientists have been so receptive to understanding the range of what we need and creating the setup to get that.”
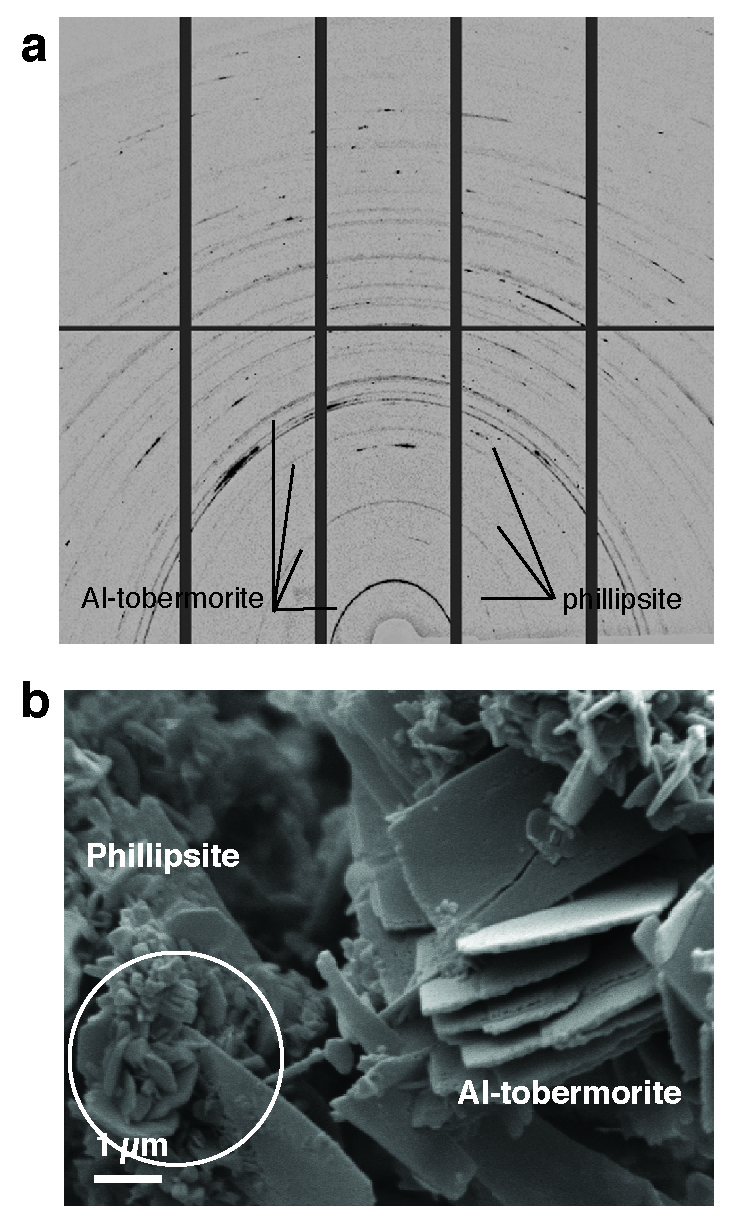
Jackson and her team of graduate student researchers have worked extensively with ALS beamline scientists Martin Kunz and Nobumichi Tamura to tailor their data analysis setup, which is the most time-intensive and challenging component of their research. In order to get the information Jackson and her team needed, Kunz said the challenge was to “find the optimum beam angle of not too steep and not too grazing.” He explain that “if you’re too flat in the incident angle you have a big footprint of the beam and you lose spatial resolution, and since Marie [Jackson] wanted to identify the nano-sized phases with high spatial resolution, we had to play around to find the optimal combination.”
“It’s extraordinary,” Jackson says. “We thought the Al-tobermorite occurred only in relict lime clasts but it turns out there’s Al-tobermorite throughout these different volcanic ash microstructures and it may actually be a binding cementitious component of the system.” This cation-exchange capability of the Al-tobermorite crystals could also have other applications for the concrete industry, particularly in hazardous waste storage.
Jackson is also analyzing data from the various crystalline phases, which will yield further insight into the Roman seawater concrete systems. “We are learning that this concrete has the ability to sequester chlorine and sulphate in crystalline structures,” says Jackson. In the Roman seawater concrete, chlorine doesn’t get very far into the structure before it’s immobilized. This process is important for the modern concrete industry because chloride corrosion of steel reinforcement is a major source of decay.